Photo: Semi-Mobile Sizer Stations leverage the flexibility of truck haulage with the efficiency of conveyor haulage.
Mining is an industry that requires investing wisely and looking at all available options when considering the setup of a new plant or attempting to reduce costs in a brownfield operation. Many considerations focus around the lifecycle of a mine; how much product is in the ground? How long will it take to extract? If it’s a short lifespan, is it a worthwhile investment? These issues all arise before equipment selection comes into play, but when answering these questions, it is vital to get right mine plan from the outset. Selecting the best mining methods and equipment in the first instance ensures a more efficient and profitable long-term future for the site. Traditionally a large proportion of mines used long haul truck and shovel systems, feeding fixed crushing plants. But in many cases, more cost-effective options are available. MMD’s Semi-Mobile Sizer Stations have the same functionality as fixed plants, but with additional advantages and lower setup costs.
Semi-Mobile Sizer Stations for IPSC
Semi-Mobile Sizer Stations leverage the flexibility of truck haulage together with the efficiency of conveyor haulage. This provides an ideal solution for many mining scenarios where flexibility is vital, such as selective mining (blending), heavily faulted seams or irregular shaped ore bodies. Constructed in easy-to-assemble modules, Semi-Mobile Stations are relocated as the mine develops to minimise truck haulage distances, and take advantage of conveyor efficiencies. Semi-Mobile units can be relocated large distances in a matter of days using the MMD Atlas Transporter. By reducing truck haulage distances, operating costs decrease whilst also reducing carbon emissions.
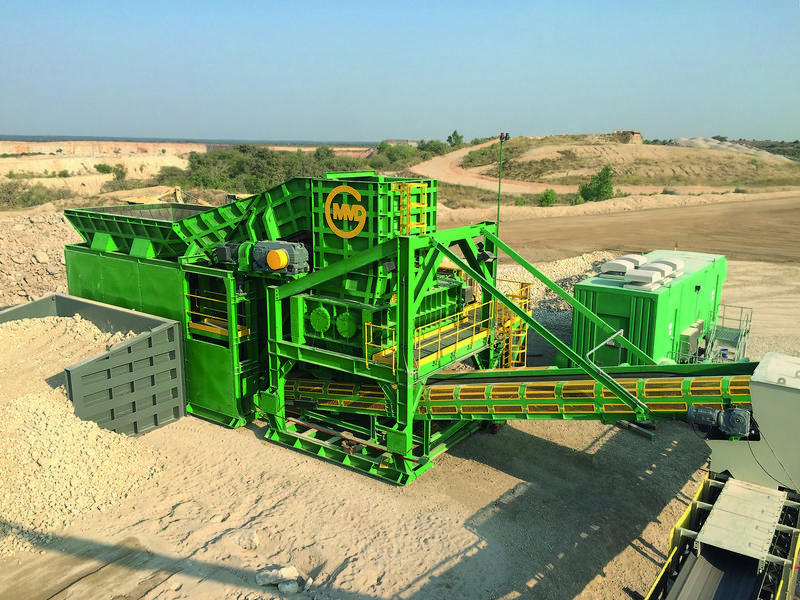
There are also some less obvious environmental advantages to Semi-Mobile Sizers Stations. Due to the Sizer’s unique features of compact dimensions and high throughput rates, a Semi-Mobile Sizer Station is significantly smaller than fixed systems, leaving less of a carbon footprint. This applies to the amount of material used as well as the time and energy used during construction.
Peripheral structures such as a concrete bunker, or RE wall and heavy duty foundations required for fixed plants are commonly not required for Semi-Mobile Sizer Stations. Semi-Mobile Stations are supported on simple pontoon-type bases. The likes of a concrete wall and foundations comes with associated labour, materials, plant and fuel costs in both the initial construction and eventual deconstruction once the mine closes. State laws often require mine owners to return the site to its original condition (or as close as possible). These often-overlooked costs can run into tens of millions of dollars. Therefore, using Semi-Mobile or mobile equipment offers a huge benefit over the life-of-mine, as there is no requirement for walls, roads and services to be removed and earth landscaped. This extra work not only costs more money, but also places an extra, unnecessary burden on the environment.
Over the last few years, we’ve seen increased interest in In-Pit Sizing and Conveying (IPSC) systems as mines seek ways to streamline operations and achieve emissions targets. Our history of delivering Semi-Mobile Sizing Stations into Southeast Asia dates back to 1993. And more recently, in 2015 we were commissioned to provide nine primary Sizing Stations to Hongsa Power based in Laos. 2018 saw the completion of three stations at EGAT’s Mae Moh mine in Northern Thailand, alongside a 400 tonne Atlas Transporter to facilitate quick and efficient relocation of the Sizer modules. With all three Semi-Mobiles operating to the satisfaction of the customer, this project is just part of the continuation of MMD’s involvement with the Mae Moh mine. We recently upgraded the mine’s Sizer Stations, previously installed in 2001, as well as providing a further Semi-Mobile Station and Transporter for the next phase of the mine’s expansion. This brings the total to eight MMD Semi-Mobiles currently operating at Mae Moh mine. In both cases, high throughputs and short relocation times make these Sizing Stations a key part of the mine’s future. MMD’s solution has lowered the operating cost of moving overburden.
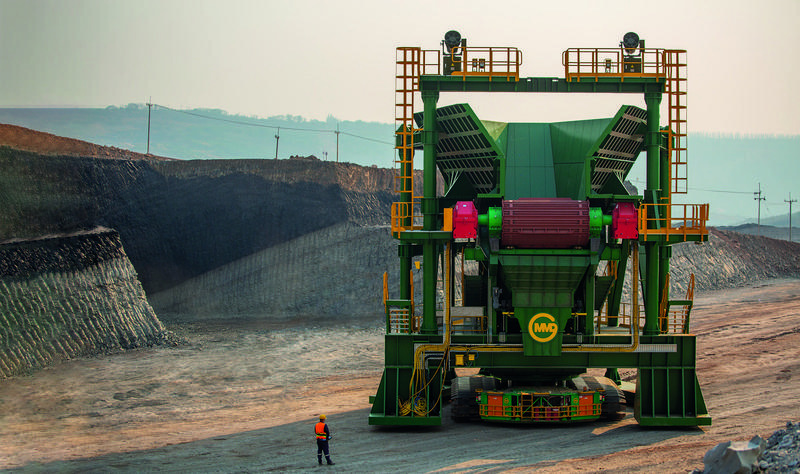
With MMD Sizers becoming more and more proficient in hard rock applications, there is an ever-increasing number of materials in which Sizers have proven to be successful. To date, we process over 80 different minerals including the likes of copper, cobalt, nickel, iron ore and gold. But with ore grades declining, it is becoming increasingly important to maximise ore recovery in the most cost-effective manner possible.
What’s next for IPSC
Efficient transportation and processing of ore plays a pivotal role in a mine’s economic and environmental strategy. Bulk Ore Sorting is the process of separating valuable ore from waste, and is an area in which gains can be made.
By separating ore from waste earlier in the mining process, only valuable material is hauled from pit to plant. Besides the obvious savings in haulage costs, efficiencies are made through less energy and water usage in downstream equipment. Ore sensor technology is already widely used in processing plants, however, MMD’s Bulk Ore Sorting systems have revolutionised the separating of ore from waste by enabling the deployment of sensor-based sorting in the pit and close to the mine face. By utilising the latest material scanners, with near real-time ore sampling, mines can expect an ore grade uplift of up to 20%. This results in a potential for lower grade cut-offs and increased ore recovery.
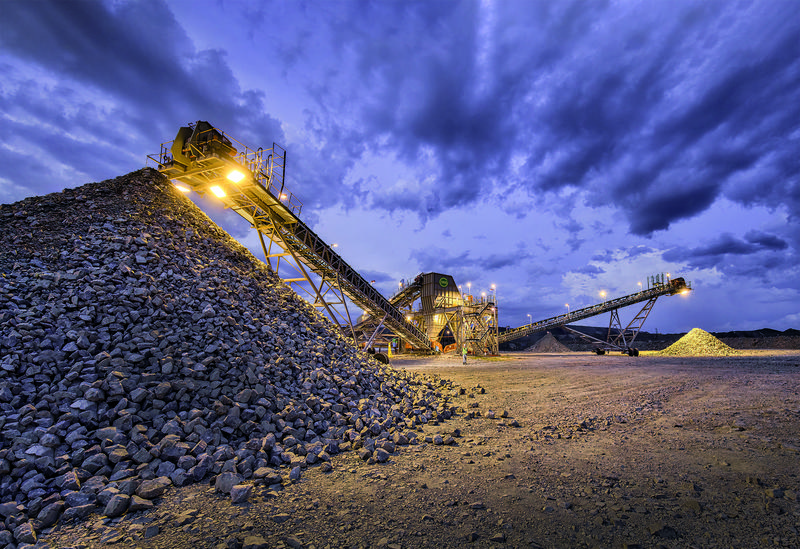
Utilising an MMD Sizer over other forms of crusher delivers some clear advantages when it comes to ore sorting. Sizers can process any combination of wet, dry, sticky or hard material through the same machine, which is ideal for processing raw material directly from the mine face. The product size is controlled in all three dimensions, whilst keeping fines to a minimum. By creating a cubical product with very little dust, the reliability and accuracy of the ore sensing equipment improves dramatically. Furthermore, by being compact and lightweight, Sizers require very little supporting structure and offer unrivalled installation flexibility – making them the ideal choice for Semi-Mobile equipment dispatched close to the mine face.
MMD have three Bulk Ore Sorting systems currently in operation, working with a variety of materials from soft and sticky nickel ore, to copper ore, and hard platinum ore. MMD's ore sorting technology is scalable can be applied using a wide range of IPSC systems. Whether it be a Fully Mobile or Semi-Mobile installation, our systems are tailored to match the throughput, material, sensors, grades and relocation methods required by each individual application.