Considered a mix of science and art, flotation is the most widely used process for extracting vital minerals in the modern mining operation. As the amount and type of froth changes from cell to cell, the best recovery systems must be able to accommodate variable froth conditions, otherwise valuable materials end up being lost to tailings.
Newer technologies eliminate the guesswork previously associated with flotation, and the latest advancements allow for adapting to the unique conditions within each cell. This improves control of the froth phase and directly affects the mine’s ability to recover either higher volumes or higher grades.
As a leading innovator in froth recovery, FLSmidth has created a Froth Recovery Upgrade package that provides customers with more control, resulting in better overall metallurgical performance. The package includes four critical technologies:
- A level sensor with a robust design and no moving parts, which accurately senses the depth and level of slurry within the cell.
- Actuators that receive data from the level sensor and adjust the dart valve position to maintain slurry levels.
- Radial froth crowders to reduce top-of-froth surface area and facilitate movement to the nearest radial launder.
- Froth cameras, which measure the froth’s velocity and stability and can also infer the froth grade.
Ideally, a flotation operation would utilise all four technologies to achieve optimal recovery; however, the full package can be segmented and installed as individual components, based on customers’ needs. This flexibility, and the real-world customer results, are illustrated by the examples below.
Customer 1 – Level Sensor and Actuator
A large copper mine in Peru approached FLSmidth to increase recovery in an 8-cell flotation bank. The mine’s existing equipment for monitoring slurry levels and controlling dart valves lacked consistency, which caused large deviations in level control. The lack of control and stability reduced overall copper recovery and had a significant impact to the bottom line.
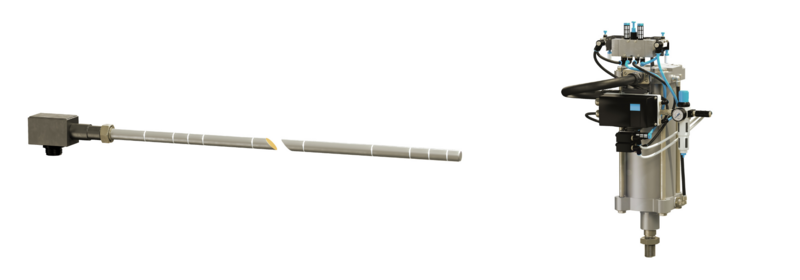
Every large fluctuation in level control resulted in two scenarios: First, the cell level would become too high, and pulp would overflow into the launders, resulting in unacceptable grade. Then the level would drop too low and result in little to no recovery of the froth phase, impacting overall recovery.
Data from the condition monitoring system revealed an opportunity for improvement, as shown in Figure 1. Sporadic movement of the actuator (blue) caused unstable deviations to the slurry level (green), causing it to fall short of the target level (yellow) needed for optimal performance.
FLSmidth engineers recommended installation of new level sensors and FESTO actuators. The customer agreed to replace its current equipment, and the upgrade yielded immediate improvements. Following the retrofit, slurry levels showed significantly higher stability and remained consistent within the target level, shown in Figure 2.
After a month with the new equipment, slurry levels consistently remained on target. As a result, the customer recovered 0.5% to 0.8% more copper than previously possible with the older equipment. Based on the short-term results, the customer anticipated replacing the remaining flotation cells in the entire plant with new level control. The mine’s return on investment was less than three months.
Customer 2 – Adjustable Radial Froth Crowders
Another copper mine in Peru consulted with the FLSmidth Flotation team to improve its froth phase control and improve performance of its rougher flotation circuit. The customer was seeking a low-capital solution using its existing equipment and opted to install FLSmidth’s Adjustable Radial Froth Crowders.
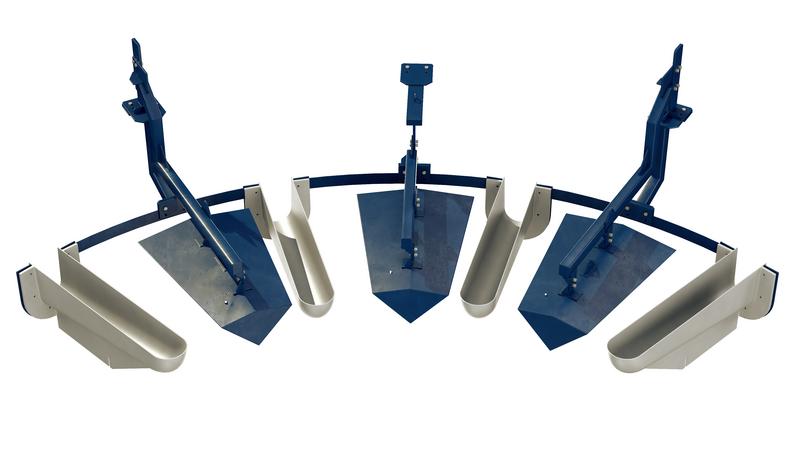
Installation of the crowders required no cutting or welding and was completed during a scheduled downtime. With no required permanent structural changes to the cell, modifications could easily be reversed if the customer chose.
After installation of the package on just one row of its rougher flotation cells, the customer noticed significant improvements to its operation. Operators were able to decrease reagent consumption, increase the froth phase depth by 3 to 10 cm, and ultimately improve the downstream operations by stabilising concentrate mass flows. With the economic gains seen from the retrofit’s improved performance, the mine retrofitted the remaining two concentrator plants with the same type of adjustable radial froth crowders.
Customer 3 – Froth Camera
A mine in western Canada contacted FLSmidth with concerns about frequent variations in its copper grade, along with low recovery numbers in its flotation circuit. FLSmidth determined that the frequent variations were caused by poor setpoint control and selection, and that a software solution would provide immediate benefits without a large capital investment. The three-part solution utilised a combination of Model Predictive Control (MPC), fuzzy logic and FLSmidth’s newest technology in froth vision systems, to improve recovery by 4% at the desired grade with less variation.
The first step was to ensure stabile level control throughout the flotation circuit. This was accomplished by controlling the dart valve positions directly using an MPC controller which greatly reduces setpoint error and variation. This process ensures that when a level setpoint is sent to a cell, that the dart valve position will be adjusted to reach the desired level set point in a quick and efficient manner.
A mine in western Canada contacted FLSmidth with concerns about frequent variations in its copper grade, along with low recovery numbers in its flotation circuit. FLSmidth determined that the frequent variations were caused by poor setpoint control and selection, and that a software solution would provide immediate benefits without a large capital investment. The three-part solution utilised a combination of Model Predictive Control (MPC), fuzzy logic and FLSmidth’s newest technology in froth vision systems, to improve recovery by 4% at the desired grade with less variation.
The first step was to ensure stabile level control throughout the flotation circuit. This was accomplished by controlling the dart valve positions directly using an MPC controller which greatly reduces setpoint error and variation. This process ensures that when a level setpoint is sent to a cell, that the dart valve position will be adjusted to reach the desired level set point in a quick and efficient manner.
Summary
With these advanced level sensors, actuators, radial froth crowders and froth cameras – installed individually or combined as a package – FLSmidth has proven its technology will allow for quicker reactions to flow and slurry density changes, greatly improving the performance of flotation machines. Better froth phase control methods can not only improve metallurgical performance in existing operations, but also allow performance prediction in greenfield operations.