Photo: The existing grates within the SAG Mill were pegging. Critical size grinding media were blocking apertures, reducing throughput
A gold and copper mine in South East Asia was experiencing a range of challenges with its SAG mill that were hitting productivity. Facing a significant increase in ore hardness that would have exacerbated the problems, the mine turned to us to provide a solution for a safer and more productive grinding operation.
A multifaceted mill challenge
A remote copper and gold mine in South East Asia had a problem: its 34 ft SAG mill was experiencing a range of performance issues that were limiting its production performance:
- Pulp dischargers of many parts. The steel dischargers on the SAG mill comprised 187 pieces. Not unsurprisingly, this led to lengthy downtimes for component replacement. Making the situation worse: the discharger service life was a relatively short 12 months.
- Inadequate liner service life. The SAG mill’s steel liners were failing to meet the required service life. To remedy the problem, the supplier had added more material to the liner design. But this created its own challenges, reducing the effective grinding volume and adding weight to the mill that was pushing bearing pressures dangerously close to limitations.
- Peening liners. The steel used to make the liners produced a significant amount of peening. This made liner removal a time-consuming activity and more hazardous activity, as a heat lance is needed to remove peened liners. It also increases the risk of structurally damaging the mill’s shell.
- Pegging of the grate plates. There was excessive pegging of the grate plates by worn metal grinding media, reducing flow. As temporary measure, the mine was cutting out the pegged media every few weeks. Which only increased the time and cost spent on mill maintenance.
To solve these challenges, the mine issued a request for quote to three companies with the challenge to improve the safety of mill maintenance and increase mill discharge. In practice, this meant reducing the number and length of maintenance interventions, as well the need for hazardous installation manoeuvres, lowering mill weight and eliminating flow constraints, such as clogging and pegging.
The beginning of the solution is understanding the problem
The journey to our solution began with a thorough review of operating conditions and liner design. Through this, we determined the first course of action should be to tackle the problems associated with the discharge system. This would allow us to increase throughput and reduce weight – and would also lead to other objectives being met.
With some key improvements in mind, we created sophisticated DEM simulations to help evaluate what discharge design would best meet the mine’s objectives. These simulations allowed us to beat the mine’s throughput target of 2,100 tpd and forecast a maximum possible throughput of 2,300 tpd. The new simulated design also showed a significant increase in service life, meeting the need to reduce maintenance interventions.
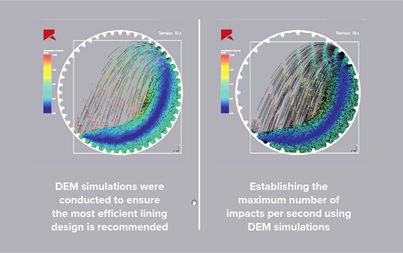
After initial onsite discussions, mine personnel were invited to review the design adjustments and define the final scope. This made sure customer knowledge was also incorporated into the solution, as well as those of our engineering team.’
Exceeding expectations
Our solution centred on our PulpMax™ composite mill liners, which were combined with material and design modifications to the steel lining system to promote increased efficiency and service life. The new liners boast 27% fewer parts (136 vs 187) and 45% lower weight (106,130 kg vs 191,962 kg).
- Made from material that is up to 50% LIGHTER. This makes the liners easier to handle and improves worker safety. Lighter materials allow us to engineer larger components at reduced weight. It also results in less parts.
- They typically have 50% FEWER PARTS. This results in a faster reline speed and quicker installation, and this adds up to workers spending less time in a confined space performing hazardous work.
Along the journey, we were also able to provide solutions to other challenges – for example, pegging of the grates and peening of the discharge steel. The result was a solution that exceeded original expectations:
- Improved safety. Fewer pieces and lower weight make maintenance simpler and quicker. This reduces the amount of time that workers spend on the mill – improving safety. It also lowers the total cost of ownership. Compounding these benefits, PulpMax composite wear liners last much longer than previous liners – through some 25 million tonnes of production. Liner service life has therefore been extended from 12 months to 15 months and based on wear measurements, could extend to 18 months.
- Improved throughput. The new system consistently achieves throughput of 2,250-2,300 tpd, exceeding the target of 2,100 tpd. This results from:
- Reduced liner mass (>100 tonnes)
- Improved shell design
- Improved discharge efficiency
- Less clogging and pegging