By Wei Wei, Product Manager, and Ricky Chua, Sales Manager, Fluke Calibration, Fluke South East Asia Pte Ltd
Calibration plays a pivotal role in the mining industry, ensuring safety, enhanced productivity, and adherence to regulatory compliance standards. As the Philippines mining sector strives to meet increasing demands, accurate calibration of equipment becomes more critical than ever. This article explores the importance of calibration, the essential tools and maintenance practices required to support calibration, the benefits of digital documentation, and best practices for control systems maintenance, providing expert insights to help mining companies optimize their operations.
Key Benefits of Calibration
Safety is paramount in mines, where workers are often exposed to high-risk environments. Properly calibrated equipment, such as pressure wells and temperature switches, function accurately, thereby safeguarding workers. This is essential in the high pressure and high temperature environments of mines. Regular calibration helps prevent accidents, making the mining environment safer for everyone involved.
Calibration also plays a crucial role in reducing unplanned operation downtime, optimizing operations and lowering costs, which leads to higher productivity and better resource management. Yields rates are significantly boosted as the ability to take accurate measurements improves control over processes such as crushing, grinding, and flotation, essential for maintaining a high production yield.
Mines must comply with predetermined regulatory standards, both in terms of environmental protection and quality. Failure to comply can result in the shutdown of the mine. Environmental compliance requires the accurate monitoring of emissions. The calibration of instruments ensures the reliable reporting of accurate data that supports compliance with industry standards.
This is all important because, with mining being at the top of the supply chain, disruptions in mining operations has a knock-on effect throughout the downstream supply chain, with concerning economic consequences. It is essential that mines optimize processes to minimize downtime, and the key to this is to apply a predictive maintenance framework.
Maintenance Practices for Ensuring Consistent Output
Predictive maintenance is an advanced approach that uses historical data and regular inspections to predict potential equipment failures before they occur. The first step is to schedule regular equipment checks. Over time, data is collected to establish benchmarks and detect patterns that can signal potential equipment failure before any physical signs become evident. This early detection of symptoms allows for the implementation of proactive measures, lowering the cost of repairs and extending the equipment lifecycle. Ultimately, the collection and analysis of this rich pool of data not only prevents unplanned downtime but also optimizes calibration intervals, ensuring equipment is always operated at peak efficiency.
Continuous training and development of the workforce are also essential practices to employ to maintain calibration standards. Regular training sessions keep workers updated on the latest techniques and technologies, enhancing their ability to perform calibration tasks accurately. Cross-training workers in multiple disciplines further increases operational flexibility and ensures continuity during shift changes.
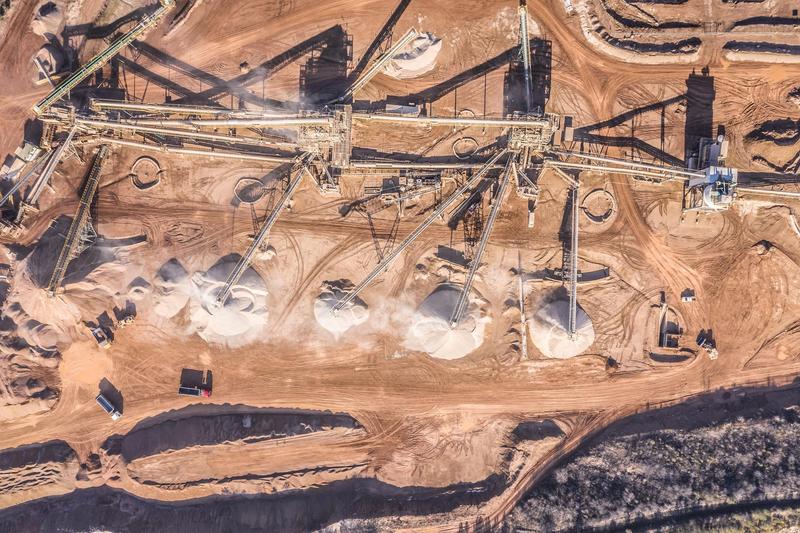
The Move to Digital Documentation
The manual recording of calibration data is impractical as it is highly labour-intensive and involves the collection and physical storage of high volumes of data. Digital documentation has become increasingly important with the rise of automated sensors in mining operations. This method involves electronically recording and storing the information collected within the calibration tool itself. Information captured includes the reading results, date of calibration, operator’s details and records of adjustments made. Digital documentation also removes the risk of human error as data collection is automated.
Digital records also support compliance with industry standards such as ISO 17025, which specifies the requirements for the general competence of testing and calibration. Maintaining a complete calibration history for each instrument across its lifecycle is crucial for traceability and audits, especially when investigating accidents. Being able to audit and identify causation leads to better practices baked into the mining operations moving forward.
Supporting a "Carry Less, Do More" Mindset
The introduction of multifunction calibrators has revolutionized the calibration process in mining operations. These devices combine the capabilities of several single-function instruments into one, significantly enhancing efficiency and reducing the physical burden on workers. An example is the Fluke 754 Documenting Process Calibrator with HART communication, which can measure pressure, temperature, and electrical signals with a single handheld device weighing only 1.2 kg and can be easily carried in a bag. The battery-powered device with its built-in interface is designed for portable use and actually performs better in its battery-powered mode.
Multifunction calibrators like the Fluke 754 enable workers to perform various calibration tasks with a single device, reducing the need to carry multiple pieces of instruments. This innovation not only enhances efficiency but also improves overall productivity. “In the past, workers had to carry multiple devices, each weighing up to 1 kg,” explains Wei Wei, Regional Product Manager, Fluke Calibration, Fluke South East Asia Pte Ltd. “Now, with multifunction calibrators, they carry just one instrument which can be up to a third of the weight of the multiple devices they had to carry previously. This makes a huge difference when factoring in the time and distance these devices need to be carried.”
Best Practices for Control Systems Maintenance
Routine Testing - Regular testing of control systems, including Programmable Logic Controllers (PLCs) and Supervisory Control and Data Acquisition (SCADA) systems, is vital for smooth operations. These systems act as the brain of mining operations, and their failure can have significant impact. Routine testing is crucial to ensure control systems don’t break down.
Emergency Handling - An up-to-date emergency response plan is essential for handling unexpected system failures. This plan should be in continual development, based on lessons learned, and should include detailed steps for troubleshooting and restoring operations quickly.
The Fluke 773 Milliamp Process Clamp Meter is an example of a tool that aids in both routine testing and emergency handling. It can measure signals without shutting down the control system and acts as a loop power source during troubleshooting.
Calibration is fundamental to the safety, efficiency, and regulatory compliance of mining operations in the Philippines. By investing in modern calibration tools, implementing predictive maintenance practices, and adopting digital documentation, mining companies can optimize their operations and ensure consistent delivery of essential materials. Prioritizing calibration not only enhances productivity but also positions companies as leaders in the industry, ready to meet the demands of a growing market.