By Sukumar Dhanapal, Regional Sales and Product Manager – Fluke Process Instruments, Fluke South East Asia Pte Ltd
In the mining and industrial sectors, where coal and other combustible materials are critical raw inputs, fire is a real and present danger. Whether coal is being transported by truck, moved along conveyor belts, or processed inside rotary kilns at extreme temperatures, the potential for spontaneous combustion or equipment overheating can turn a routine operation into a crisis in minutes.
This article looks at how real-time thermal monitoring and advanced fire prevention systems can help detect hotspots before fires start, protecting people, preserving assets and maintaining uninterrupted production.
The Heat Is Always On
Coal may seem inert on the surface, but under pressure or in hot conditions, it can ignite without warning. Trucks transporting coal across long distances must, therefore, be equipped with hotspot monitoring systems. When a PLC system receives a high-temperature alarm, the protocol is immediate: stop the vehicle, exit the cab, inspect the load and cool down the affected area with water. This simple step, triggered by early detection, can prevent a catastrophic fire.
Conveyor belts pose another significant hazard. These rubber-lined systems are essential to bulk material handling, yet they are highly vulnerable. As coal travels over them, the friction and pressure can generate hotspots. If left unchecked, these can lead to fires that damage both equipment and infrastructure. That is why thermal scanning systems, mounted directly above the conveyors, are critical. Edge-to-edge infrared, thermal line scanners from Fluke Process Instruments continuously monitor belt temperature and set off the alarm when thresholds are exceeded.
Around-the-Clock Yard Monitoring
Once coal reaches a storage site, the risk does not end. In fact, open yards, especially in hot weather, can be high-risk zones. Large coal piles trap heat internally and, if not monitored, can smoulder undetected for hours before bursting into flames. Fluke offers robust infrared thermal solutions that deliver 24/7 real-time monitoring, ensuring early detection and timely intervention. These systems alert plant operators instantly when a hotspot develops, enabling immediate water spraying or other corrective action.
Inside the Kiln: High Stakes and Higher Temperatures
Coal is also a vital fuel in the manufacturing sector, used in rotary kilns that can operate at up to 1,600°C. Though the surrounding refractory bricks can withstand temperatures up to 2,000°C, prolonged exposure and constant use make kiln interiors particularly vulnerable to hotspots. Any unexpected spike in temperature can damage the kiln, requiring a full shutdown and repairs that can take a month or more, leading to significant production losses.
CS400 kiln shell infrared process monitoring system from Fluke Process Instruments is specifically designed to meet this challenge. Installed at a midpoint along the kiln’s length, the scanner tracks the surface temperature as the kiln turns. It can precisely locate hotspots and monitor the kiln’s RPM to detect anomalies in operation. Its built-in video functionality allows operators to view live footage from inside the kiln, while advanced reporting capabilities provide valuable insights for maintenance planning.
Pyrometers and Thermal Imaging: Seeing the Invisible
In areas where the scanner’s view is blocked due to structural pillars or internal objects, the solution is advanced pyrometers from Fluke Process Instruments. These devices measure the temperature of shadowed areas and integrate seamlessly with the scanner system. Built for rugged environments, the pyrometer is enclosed in a specially designed thermal jacket and mounted on a bracket with full 360° rotation. An air purge system protects the lens from dust and debris, ensuring reliable data collection.
To manage internal heat exposure, the system also activates cooling fans based on real-time temperature readings, helping extend the life of both the kiln and the monitoring equipment. All devices can be configured to work with different communication protocols, including Siemens Profinet, Ethernet/IP, and Standard ASCII/HTML, ensuring seamless integration with existing control systems.
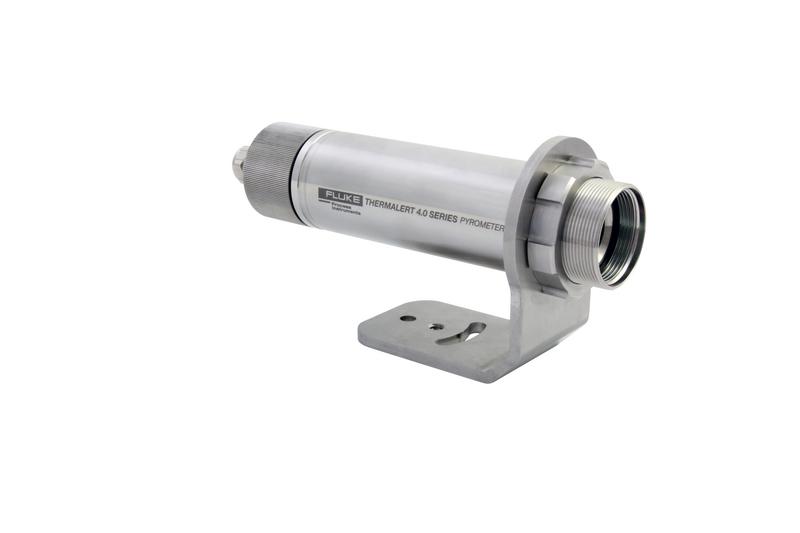
Proven Success, Global Reach
Over the last 20 years, Fluke has completed more than 500 installations of these monitoring systems in mining and manufacturing facilities worldwide, with zero reported failures. Each system is tailored to the client’s needs, from sensor placement to software integration. Fluke engineers work closely with on-site teams to ensure the hardware, communications equipment and data outputs are fully aligned with operational requirements.
Fire Prevention Is Smart Business
Fire safety helps to ensure operational continuity, protect assets and secure the bottom line. Whether it is a conveyor system in a coal yard, a rotary kiln in a cement plant, or a fleet of haul trucks in the field, proactive thermal monitoring is the frontline defence.
With intelligent scanning, pyrometry and thermal imaging systems from Fluke Process Instruments, industrial operators gain peace of mind, and the actionable data needed to prevent fires before they ignite. In high-heat environments, there is no second chance to stop the spark.